EV Wire Harness Trends: A Revolution in Design
The rise of electric vehicles (EVs) is a major force in automotive wiring innovations.
EVs and hybrids require complex wiring systems to manage high-voltage electric drivetrains, batteries, and advanced electronics. These systems necessitate specialized harnesses that can handle increased voltage and intricate connections for electric propulsion.
The demand for these wire harnesses is projected to rise significantly over the next decade. This growth is fueled by several factors, including the proliferation of advanced driver assistance systems, stricter government regulations, the expanding connected car ecosystem, and the greater integration of communication devices in vehicles.
Here are the five EV trends we’re noticing in automotive wire harness design industry:
1. The growing demand for advanced safety and comfort features
Advanced Driver Assistance Systems (ADAS) and crash safety features require sophisticated and robust wire harnesses to manage high-speed data transmission and reliable power connections. The integration of Vehicle-to-Everything (V2X) communication also necessitates wire harnesses that support reliable connectivity and data exchange.
Comfort features such as infotainment systems, climate control, and power-adjustable seats add to the complexity, requiring extensive and efficient wiring. To accommodate these features without increasing vehicle weight, wire harnesses are being designed to be more compact and lightweight, using thinner wires, advanced materials, and optimized routing strategies.
Ensuring durability and reliability is essential, which drives the adoption of high-quality materials and advanced manufacturing methods. Furthermore, the flexibility of modular and scalable wire harness designs facilitates straightforward upgrades and customization, accommodating various vehicle models and trim levels. These developments collectively enhance vehicle safety, comfort, and contribute to the ongoing advancement of automotive technology.
2. Fiber Optics: High-Speed Data Transfer and Connectivity
Fiber optics are increasingly pivotal in electrical vehicle wiring, particularly for their capability in high-speed data transfer and connectivity needs. Unlike traditional copper wires, fiber optics offer significantly higher bandwidth and data transmission speeds, making them indispensable for handling large volumes of data swiftly and reliably.
This capability is crucial for powering advanced driver assistance systems (ADAS), infotainment setups, and vehicle-to-everything (V2X) communication, enabling real-time data processing essential for autonomous driving functionalities and dynamic traffic updates. Fiber optics also exhibit superior resilience to electromagnetic interference (EMI) and signal degradation over long distances, ensuring consistent performance and data accuracy in diverse automotive environments. Their integration supports seamless connectivity within ADAS networks, enhancing the precision of safety features like collision avoidance and lane-keeping assistance.
3. Modular Wiring Systems for Customization
Modular wiring systems are transforming EV wire harness design by enabling increased flexibility and customization capabilities. These systems use prefabricated modules or segments of wiring that can be easily interconnected or replaced, accommodating various vehicle configurations and optional features. This adaptability simplifies manufacturing processes and speeds up assembly lines. Each module undergoes rigorous testing and adheres to standardized specifications, ensuring consistent quality and reliability across different vehicle models and production runs. Maintenance benefits from modular designs, making servicing easier by allowing individual modules to be replaced without extensive disassembly. In turn, this reduces downtime and repair costs.
In terms of cost efficiency, while initial setup expenses may be higher due to module development, long-term savings are achieved through streamlined assembly procedures, improved inventory management, and simplified aftermarket servicing. Modular systems also empower automotive manufacturers to swiftly incorporate new technologies, such as ADAS and connectivity solutions. This capability ensures vehicles remain competitive and compliant with evolving regulatory standards. Ultimately, modular wiring systems play a vital role in enhancing production efficiency and enabling EVs to meet diverse consumer preferences and technological advancements effectively.
4. Smart Wire Harnesses
Smart wire harnesses with integrated sensors use real-time data collection and analysis to forecast potential faults and issues in EV electrical systems. This proactive approach enables vehicle systems or maintenance personnel to detect early warning signs and take preventive actions, such as inspecting and repairing problematic areas before they lead to critical failures. As a result, this predictive maintenance strategy reduces downtime, enhances vehicle reliability, and effectively lowers overall maintenance costs. Ultimately, these advancements contribute to improved vehicle safety and performance by addressing potential issues proactively before they affect vehicle operations.
5. Environmental Sustainability in Wiring Harness Production
The focus here is on minimizing the environmental impact throughout the entire harness lifecycle. This means using eco-friendly materials, such as recycled plastics, and lightweight options to reduce a vehicle’s footprint. Additionally, manufacturers are optimizing production to minimize waste and using renewable energy sources. Finally, designing harnesses for easier disassembly allows for proper recycling and reduces landfill waste. These practices pave the way for a greener automotive industry.
Why Automation is Key to Wiring Harness Production for Electrification
EV wire harnesses and other EV electrical systems are becoming a production bottleneck. For starters, EVs require nearly double the wiring of fossil-fuel cars. Traditional, manual production struggles to keep pace with the sheer volume and intricate nature of EV wiring. Unlike standard harnesses, EV versions manage separate high-voltage systems for batteries and motors, adding layers of complexity. The growing scarcity of skilled labor further tightens the knot.
Automation emerges as the hero, untangling this wiring maze. New approaches integrate electrical functionality directly into components, leading to lighter and more compact designs. Imagine 3D-printed parts with built-in wiring, eliminating waste and the need for oversized cables.
The benefits extend beyond efficiency. Automation unlocks a completely digital design process. Imagine seamlessly integrating electrical functions onto any surface, curved or flat. This empowers manufacturers to push the boundaries of EV design and extend this approach across various industries reliant on electrical functions.
Electrification’s success hinges on the ability to produce these complex harnesses. Automation, with its ability to handle increased volume, lighter harnesses, and complete design digitalization, is the key to unlocking electrification’s full potential and a cleaner future.
How Smart Wire Harness Manufacturing Can Boost the EV Market
Smart wire harness manufacturing holds significant potential to enhance the EV market through several key advancements:
1. Advanced Data Analytics
By integrating sensors and data analytics into wire harness manufacturing, manufacturers can gather real-time insights into production processes. This allows for continuous monitoring of quality metrics, production efficiency, and predictive maintenance of equipment. For the EV market, this means improved reliability and quality assurance in harness production, leading to enhanced vehicle performance and durability.
2. Integration of IoT and Industry 4.0
IoT (Internet of Things) technologies enable connectivity between machines, systems, and processes within the manufacturing environment. In the context of wire harness manufacturing for EVs, IoT facilitates seamless communication and data exchange between assembly line components. This integration supports adaptive manufacturing processes, where production systems can dynamically adjust to optimize efficiency, reduce downtime, and enhance overall productivity.
3. Sustainability and Environmental Impact
Smart wire harness manufacturing also contributes to sustainability goals within the EV industry. By optimizing energy usage, minimizing material waste through advanced production techniques like additive manufacturing and recycling initiatives, manufacturers can reduce the environmental footprint of harness production. Sustainable practices not only align with regulatory requirements but also appeal to environmentally conscious consumers, bolstering the market appeal of EVs
From Design to Manufacturing, Arcadia’s Role in Advancing Innovation
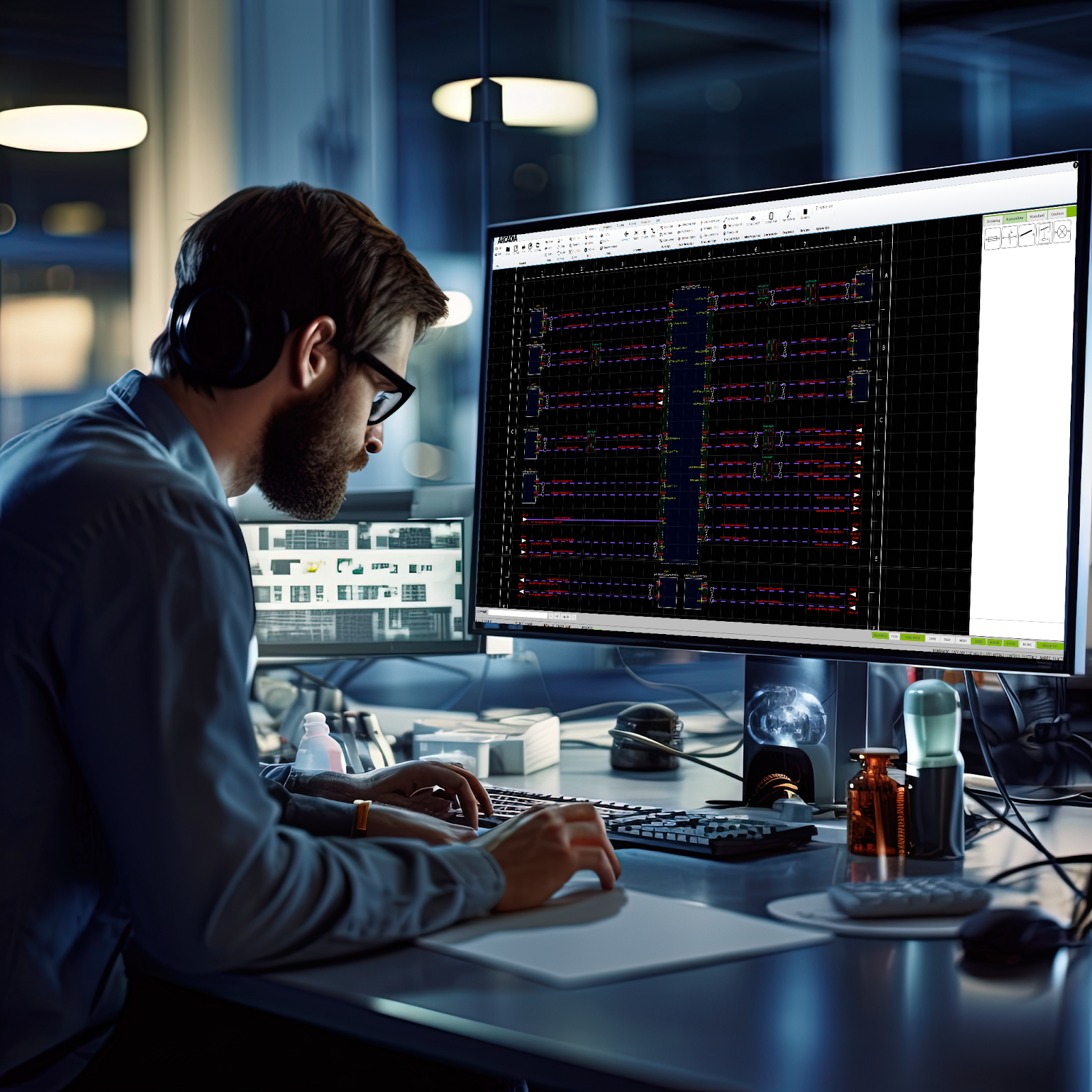
Arcadia’s suite of cloud-based software is designed for engineers by engineers to help you address automotive wire harness design for EVs easily and quickly. By incorporating Arcadia software early in your design, you can significantly enhance efficiency, mitigate errors, and achieve seamless integration into manufacturing processes.
Ask us for a free demo
We’re happy to give you a free demonstration of our innovative solutions, so you can see the results for yourself. If you have any questions about how to EV wire harness trends and how we can help, we’re always happy to assist you.
