Designing wire harnesses for harsh conditions and demanding environments requires a deep understanding of the specific challenges involved. Extreme temperatures, moisture, chemicals, mechanical stress, and electromagnetic interference are just a few factors to consider. Addressing these factors early in the design process is critical to ensuring the harnesses’ reliability, safety, and durability.
Harsh Environments and Solutions
Let’s start with the temperatures to which your wire harness is likely to be exposed.
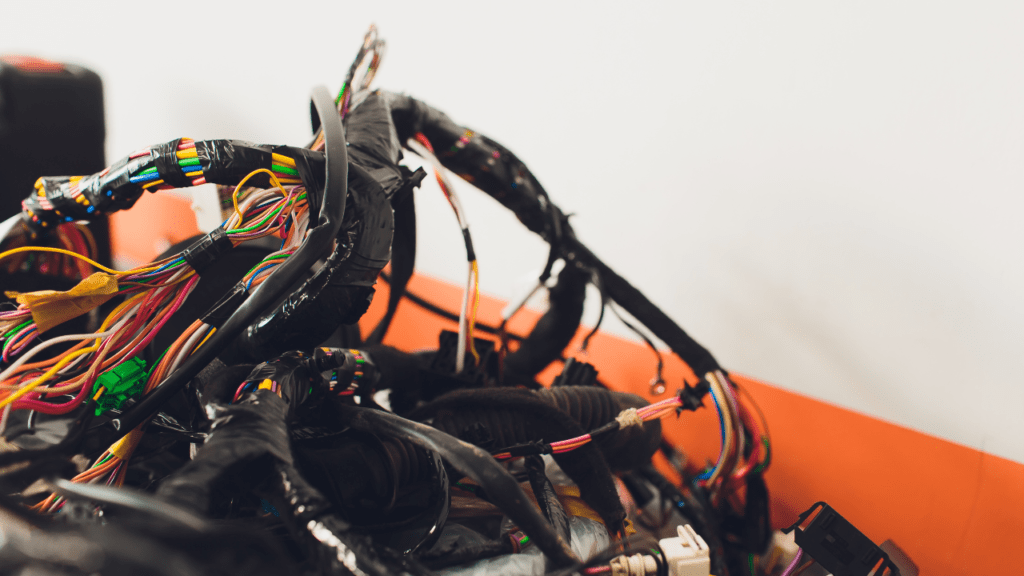
1. High Temperatures
Wire harnesses exposed to high temperatures are at risk of several issues that can affect their functionality and safety. Insulation materials may degrade, become brittle, crack, or even melt. This can lead to short circuits or electrical failures. Conductors might expand due to the heat, potentially loosening connections and causing intermittent problems.
High temperatures can speed up chemical reactions that degrade materials and lead to corrosion. In severe cases, excessive heat can cause flammable components to ignite, creating a fire risk. To address these concerns, using heat-resistant materials and incorporating effective thermal management in the harness design is important.
Solutions
- Materials: Some examples of heat-resistant materials include Polyimide (PI), Polytetrafluoroethylene (PTFE), or cross-linked polymers that can withstand elevated temperatures (up to 400°C in aerospace).
- Heat management: Apply heat dissipation strategies, such as using heat-resistant conduits, routing away from heat sources, or incorporating thermal barriers.
2. Low Temperatures
The primary concern here is the brittleness that can develop in insulation materials, making them more prone to cracking or breaking under mechanical stress. This can lead to exposed wires, which increases the risk of short circuits or electrical failure. Low temperatures can also cause materials to contract, potentially loosening connections and resulting in unreliable performance or intermittent faults.
Some materials may lose flexibility, leading to increased strain during movement or vibration, further exacerbating the risk of damage. To mitigate these risks, using materials specifically designed to remain flexible and durable in cold environments is important.
Solutions
- Materials: Suitable materials include silicone or fluoropolymers that remain flexible in cold environments. Ensure that all materials, including connectors and insulators, are rated for the lowest possible temperatures expected.
3. Moisture and Water Exposure
In environments like marine or industrial settings, waterproof harnesses are critical due to exposure to high humidity, rain, or even direct immersion in water. Moisture can seep into the harness, leading to short circuits, corrosion of metal parts, and potential electrical failure. Saltwater, particularly in marine environments, can significantly accelerate corrosion, posing an even more significant threat.
Solutions
- Materials: Use materials like Polyurethane (PUR) or Neoprene for the outer jacket to provide a barrier against water intrusion.
- Design: For waterproof harnesses, it’s essential to cross-wrap the branches, ensuring that the wiring harness remains fully covered. Where waterproof rubber rings or through-hole rubber sleeves are used, the harness should first be partially encapsulated. After that, the rubber ring or sleeve should be securely wrapped around the harness using a double-wrapping technique.
- Connectors: Opt for sealed or over-molded connectors to prevent moisture from entering critical areas. Choose connectors with an IP67 rating or higher for high-humidity or submerged environments.
- Conductors: Tinned copper or other corrosion-resistant alloys can help prevent the damaging effects of water and salt exposure. If weight is a concern, consider aluminum. Lighter than copper and used in aerospace applications, it requires special terminations to prevent galvanic corrosion.
4. Chemical Exposure
In industrial settings, wire harnesses are often exposed to chemicals, oils, and solvents, which can degrade insulation materials. This degradation can lead to brittleness, cracks, or swelling, compromising the harness’s integrity and increasing the risk of electrical issues.
Solutions
- Materials: Use insulation materials known for their chemical resistance, like PTFE, Ethylene Tetrafluoroethylene (ETFE), or Fluorinated Ethylene Propylene (FEP). Consider applying additional protective coatings to enhance resistance to harsh chemicals.
5. Mechanical Stress and Abrasion
Wire harnesses in industrial, automotive, or aerospace settings are subject to mechanical stress from vibration, movement, and abrasion. These forces can wear down the insulation, leading to exposed wires, short circuits, or even complete failure.
Solutions
- Abrasion-resistant jackets: Choose materials like cross-linked polyethylene (XLPE) or thermoplastic elastomers (TPE) that offer high resistance to mechanical wear.
- Strain relief: Incorporate components such as grommets, clamps, and cable ties to reduce stress on the wires, particularly at connection points and in areas subject to frequent movement.
- Protective conduits or flexible tubing: This will shield the harness from physical damage and reduce the impact of vibrations.
6. EMI and RFI
Wire harnesses can pick up unwanted signals or interfere with other electronic systems in environments with significant electromagnetic interference, such as near heavy machinery or in aerospace applications. This can result in data corruption, communication errors, or malfunctioning equipment.
Solutions
Use shielded cables with braided or foil shields to protect against EMI and RFI. Proper grounding of the shielding is essential to reduce noise effectively.
- Twisted Pair Wiring: Implement twisted pair wiring for signal lines to cancel out electromagnetic noise.
- Grounding: Ensure all wire harness components are grounded properly to prevent static electricity buildup, which can worsen EMI problems.
Additional Strategies when Designing Wire Harnesses for Harsh Conditions
When designing wire harnesses for use in harsh environments, it’s essential to prioritize durability and reliability. Extreme conditions require specific design strategies to ensure the system’s performance and longevity. Here are several key approaches to optimizing wire harnesses for challenging environments. We’ve already talked about some of them, but they bear repeating.
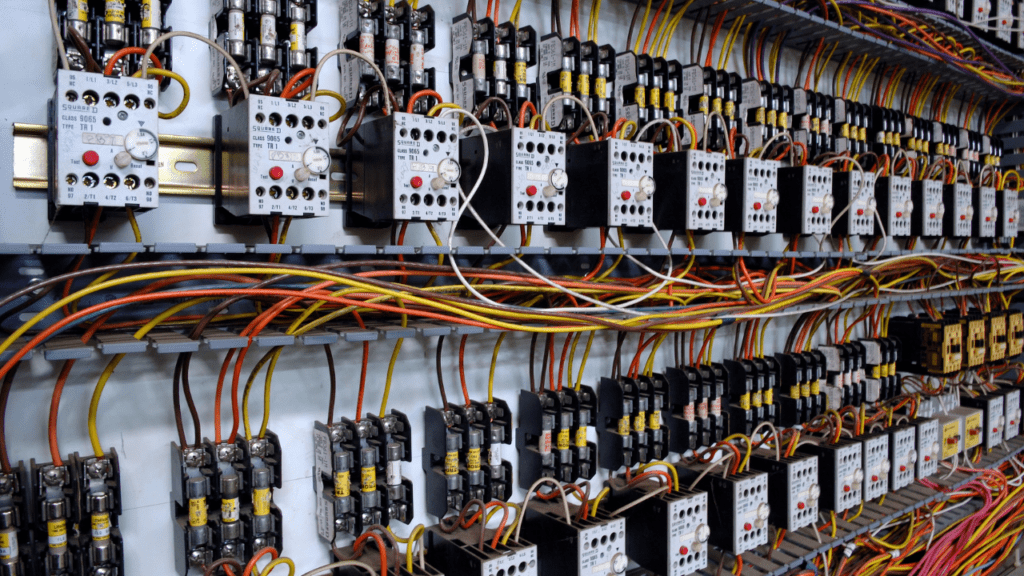
Redundancy
Incorporating redundancy into the wire harness design is essential in high-stakes applications where reliability is critical. Critical systems are safeguarded with multiple, separately routed wires by implementing parallel routing. Doing so ensures continued operation even if one wire fails, which is particularly important in industries like aerospace, where safety and system integrity are top priorities.
Minimizing Failure Points
To enhance the reliability of wire harnesses, it’s essential to reduce the number of potential failure points. You can achieve this by limiting the use of connectors and junctions, which are common sources of failure. When connectors are necessary, opting for those with a strong track record in harsh environments can further reduce risk and improve the overall robustness of the harness.
Testing and Validation
Rigorous testing and validation are key to ensuring that wire harnesses can withstand harsh operating conditions. Environmental stress screening (ESS) techniques such as thermal cycling, humidity exposure, salt spray, and vibration tests are crucial for verifying the harness’s durability. Electrical tests like hipot (high potential) testing and continuity checks are necessary to confirm the integrity of insulation and conductors.
Final Thoughts
Considering all the factors outlined above, it’s clear that you have to spend more time designing wire harnesses for harsh conditions, especially when environmental protection is involved. For more information around how you can incorporate ruggedization into your harness manufacturing process, check out our article on Creating Ruggedized Wiring for Harsh Environments. With best-in-class, cloud-based Arcadia software, you can still streamline the design and manufacturing processes. To see how you can improve your efficiency and productivity, we’re happy to give you a free demonstration. And if you have any questions, we’re here to help.
