It never hurts to remind yourself of the basics when it comes to designing your cable harness.
For your application to function as intended, every component and cable assembly must be carefully considered. This goes for your wire harness. The use of all wire harness types can improve the efficiency, reliability, and safety of a system by reducing the risk of loose connections, shorts, and other electrical problems.
Specific factors will inform your wire-harness design. Remembering what these factors are will give you a solid understanding of exactly what your application needs when it comes to your wire harness.
Getting started
Take these 10 factors into consideration to help you design your wire-harness assembly:
1. Purpose
This is indeed basic, but it’s very necessary for designing the most reliable wire harness possible for your application. What do you need your wire-harness design to do, other than transmit electrical signals and power between different components in your system?
You wouldn’t design, say, automobile wiring harnesses the same as you would a custom stereo wiring harness. Think about your application’s specific needs. For example, does it need to resist vibration? (All electronics vibrate, but an engine wiring harness has additional considerations.) Does your wire harness need to protect against electromagnetic interference (EMI)? Stand up to certain environmental conditions, such as heat or pressure?
2. Wire selection
Always review relevant standards, which provide guidance on the selection of suitable wires for specific applications. This will ensure that the wire you ultimately choose meets the necessary requirements. That said, here are the major factors to consider when designing your wire-harness assembly.
– Wire specifications
What are your electrical requirements? This is determined by the wire’s gauge or thickness. Choosing the right gauge wire demands that you consider the carrying capacity and amount of current the wire needs to conduct. This is measured in amps. Length matters too. The longer the wire, the more voltage is lost through resistance and heat. You can get around this problem by increasing your wire gauge, which of course, will increase your amp capacity.
– Environmental conditions
The suitable wire can be used easily in your application’s environment. For example, if the harness will be exposed to high temperatures, a wire with a high-temperature rating should be selected. If the harness will be exposed to moisture, then choose a wire with a moisture-resistant coating.
– Mechanical properties
Correct and efficient outputs are also determined by the wire’s ability to withstand mechanical stresses. This includes bending or twisting without breaking or losing its electrical properties. The wire should also have good abrasion resistance if it will be exposed to rubbing or scraping.
3. Wire connection
Connectors create an electrical circuit while helping to protect your wires from environmental conditions, such as abrasion and EMI.
The selection of connectors should be based on their electrical and mechanical properties. The wires themselves will influence your connectors, so you’ll need to have an idea of the wires’ material, gauge and length.
Circuit size and density, along with space limitations, should also be considered. It’s also helpful to think of the ease of joining wires and disconnecting wires if necessary. And, of course, do you need insulation?
The termination end type matters too
You’ll need the appropriate connectors for board-to-board, wire-to-wire, or board-to-wire. Give thought to your connector hardware too. Your clamping device and other hardware are used to install and support the connector, so it needs to be of excellent quality.
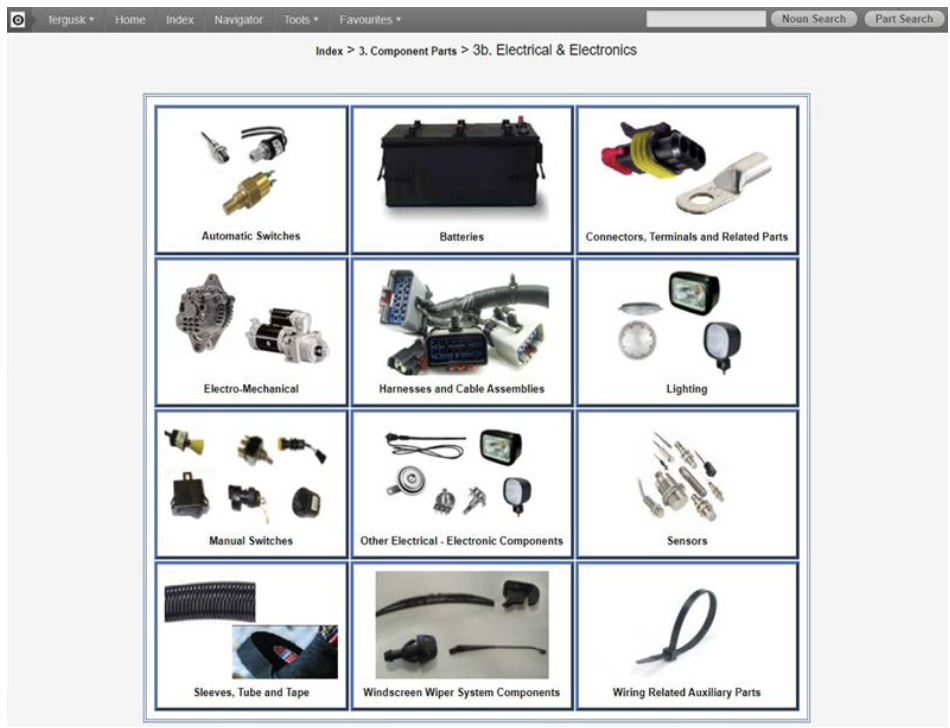
The importance of standardization
Use standard, common-use connectors and other components. It’ll make your life easier to source what you need. That said, the search can still be time-consuming, so go a step further with the cloud-based Arcadia Component Database. Not only can you search for the right parts quickly, but you can also call up the necessary documentation for components. It also helps you avoid duplication in inventory and allows your purchase team to review price details quickly.
4. Routing
The routing of wires plays a major role in successful cable harness design. First, ensure that wires are routed in a way to make accessibility easy. Optimum positioning is key. You want the harness to be easy to install and maintain. If any wires need replacing or repairing, that should be easy too.
You also need to take into account any potential sources of EMI that could affect the performance of your wiring harnesses. The routing in your cable and wire harness design should minimize the risk of interference and prevent any signal degradation.
Segregate your wires
Do this according to their function, voltage, and signal type, which will help prevent interference and ensure the wires are correctly connected to their respective devices. You want to make sure that wires are routed to the correct electrical system points.
5. Strain relief
Designing wire harness assemblies for strain relief will prevent headaches. Failure to do this can result in wires becoming loose or breaking due to vibration, pulling, or other forces. This is especially important in applications where the wire harness is exposed to high levels of mechanical stress.
Add strain-relief components if necessary
Your first task is to identify potential sources of stress. Consider cable management to help with strain relief. You can protect your wire harness assemblies with components such as grommets, cable clamps, or cable ties. Your choice will depend on the specific application, environment, and overall design of your wire harness.
Next, determine the appropriate location in the wire harness for any strain relief components. Typically, they should be placed at the points where the wires exit the wire harness, as these are normally the most vulnerable points. (You also need to ensure that the wire harness is flexible enough to allow for movement and bending as necessary, while still maintaining its structural integrity.)
Material matters
Don’t forget to consider material for your strain relief. It must be able to stand up to environmental conditions and provide the properties you need it to, such as strength or chemical resistance.
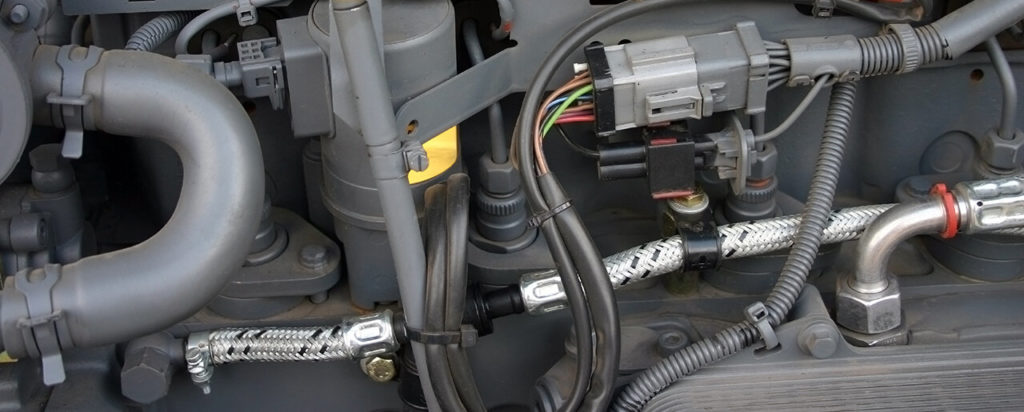
6. Wire-harness diagram
It’s critical to get it right in the early stages, so it’s advisable to not attempt your wire-harness diagram by hand. The well-designed wiring diagram is created using a good wire-harness design tool such as computer-aided design or ECAD.
Take, for example, the cloud-based, state-of-the-art Arcadia suite. It enables engineers to design and simulate electrical systems and wiring harnesses. For instance, you can check your design to see behavior and voltage drops in real-time, with just a browser, and make any necessary adjustments. You can even find out if your design meets safety standards at this stage.
Identify potential issues
With the right software – such as Arcadia Schematic – you can improve accuracy and design quality while ensuring you meet industry standards and specifications. These tools can help you identify potential issues, such as wire-to-wire interference, voltage drop, or wire length limitations, which can result in errors or quality issues.
Speeding up the design process
They also speed up the design process and significantly reduce errors and rework. Arcadia Harness, which integrates seamlessly with its schematic cousin, shows you components from every viewpoint and offers splice balancing functions with comprehensive splice diagram generation, illustrating how to construct each splice. You can add labels in your wire-harness diagram for connectors and splices.
Ensure flexibility
You need to ensure that the wire harness is flexible enough to allow for movement and bending as necessary, while still maintaining its structural integrity. The Arcadia suite enables you to do this. All of this adds up to tremendous cost savings, helping you optimize the design phase. Manual wiring harness diagrams are simply an inefficient way to work.
7. Protective covering
The wire harness should be covered with a protective sheath or sleeve to protect it from damage. Providing an extra layer of insulation will protect your wires and cables. This involves understanding the environmental conditions the wire harness will be subjected to and the material of your protective covering.
Pay attention to material properties
For example, if you’re designing a custom engine wiring harness, vibration, rattles, fluids, and chemicals will be a concern. The material for your coverage will need to handle those threats. Protective coverings vary by type, from pulled-on braided tubing (or loom) to tapes, spiral wrap, and heat-shrink sleeves, which also ensure neat wire bundling.
8. Testing
Always keep testing in mind, even in the early design stages. It’ll help keep you on your toes. Don’t overlook anything when testing your prototype, or you risk downtime at the Quality Control stage and you’re back to the design table. Make sure you have the proper equipment that can check electrical integrity. It should be able to locate faults across all conductors of the Unit Under Test (UUT) without human intervention.
You’re testing the quality of your connections. You’ll want to include embedded resistors and electrical load. Essentially, you want testing to:
- Measure resistance
- Allow you to set up limits, or dual thresholds
- Check for intermittent connections
How to save hours in testing
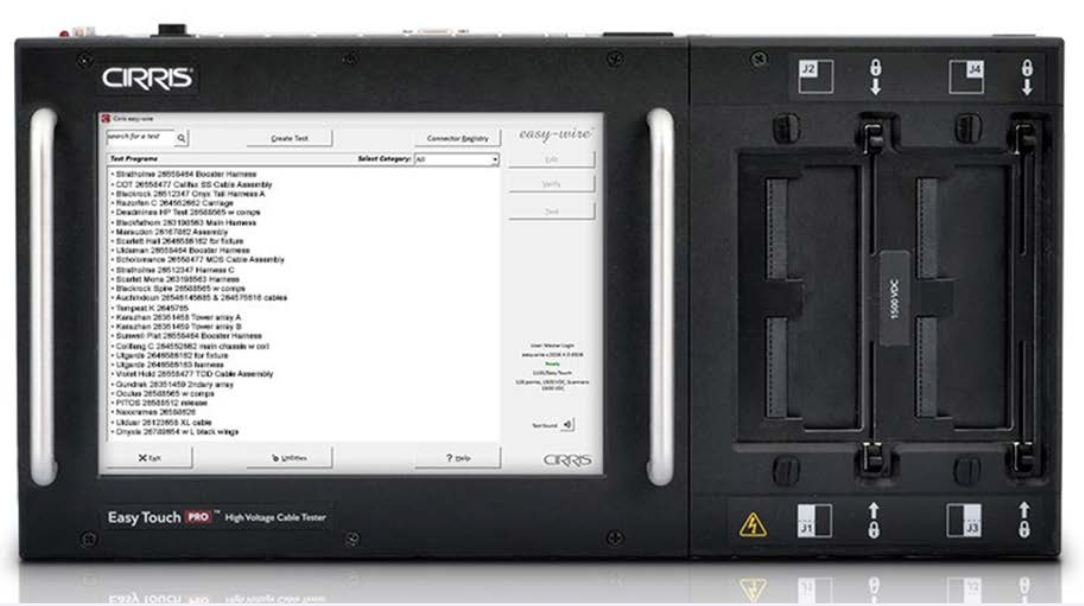
Of course, you can make it easier on yourself with Arcadia Harness Manufacturing, which provides cloud-based testing interfaces. It removes manual test code creation and entry, saving hours in the technician’s time and avoiding manual errors. It allows you to ensure that your harness builds to match your CAD 100% without having to build, learn and test against a golden sample build.
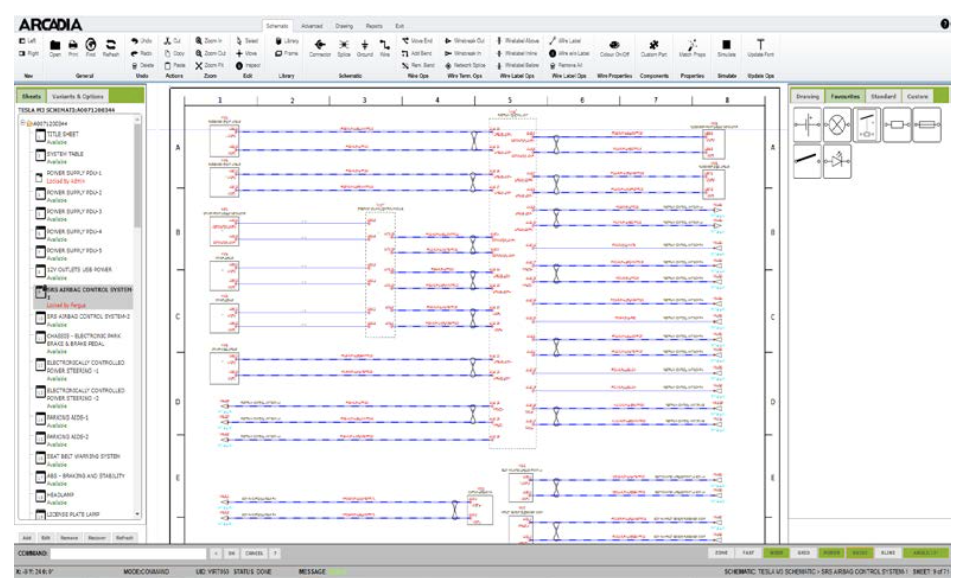
9. Documentation
Documentation is critical for after-sales & service technicians. This includes an intelligent, technical publications export that includes the schematic design and all connector information, along with locations embedded into a simple online/offline viewer. This makes your technical publications easy to generate and for your service engineers to understand.
10. Compliance
The design and manufacturing process of wire harnesses are subject to regulations and standards. Make sure that your harness design complies with these.
Regulatory and safety standard agencies
Every region enforces the testing of electrical devices. The IPC/WHMA-A-620 is the industry standard for wire harness assembly and is the predominant standard in the U.S. If your application has an international market, you might need to use one of the following as your guideline:
- IEC (International Electrotechnical Commission)
- CEE (International Commission for Rules for the Approval of Electrical Equipment)
- CENELEC (European Committee for Electrical Standardization)
7-day free trial, always free demo
Arcadia’s suite of cloud-based software can streamline your wire harness design processes, making you far more efficient and productive. Try our seven-day free trial now – it’s easy to give our solutions a spin because they work on the cloud.
On-premise software vs designing on the cloud
What’s the difference? On-premise software is installed on your computer, and that’s where it stays. It requires server infrastructure, which is typically expensive. Cloud software, known as SaaS (software as a service), is a different story. It allows you to collaborate wherever you are and share with your team so that you work more dynamically and faster, ensuring that you’re all on the same page.
Ask for a free demonstration
If you want to first see how it works, just give us a call and we’ll set up a demo. If you have any questions, we’re always happy to help. We were the first cloud-based software for wire harness design, and we continue to innovate with new offerings.